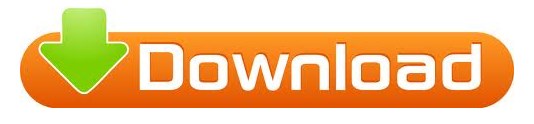
The Analysis Settings for this example were set to perform a Large Displacement analysis, with non-default Output Controls set to output contact information that would make it possible to measure the force transmitted across the contact pair in the model. The force has components in the Global X and Y directions: The edge at one end of the surface body pair was fixed, and a force was applied to the other end. Other Detail settings in the Advanced section in Figure 5 have been left as Program Determined in this example, although users may prefer to increase the Normal Stiffness factor, and to set a Pinball Region manually. The deflection plot has similar amplitude, but the stress does not show the figure above result, where “thick” region stresses are higher at outer layers, and smaller at the bonded interface, which acts like the mid-plane of an 8mm thick shell.įor this reason, the “Nodal-Projected Normal From Contact” of Figure 7 will be preferred. The figure below shows equivalent stress and Y deflection with Detection Method “Nodal-Projected Normal From Contact”.Ĭontrast this with the figure below, the consequence with “Program Determined”. The Projected choice is a relatively new addition to Ansys. Users may want to experiment with the consequences of these various choices. The figure below shows the Detection Method choices in a drop-down listing. The Detection Method has been set to “Nodal-Projected Normal From Contact” which was found to produce deflection and stress plots that were preferable to those resulting from alternative settings. In the figure below, the Formulation has been set to “Augmented Lagrangian” although a Penalty setting has also been satisfactory in testing. In the present example, a Symmetric behavior is selected. This is required to get the resulting target and contact elements in Ansys to attach to each other without implied penetration and solution failure.Ĭontinuing with the Details definition of the contact pair, the contact will be set to Bonded, which permits both Symmetric contact with penalty-based formulations, and Asymmetric contact with all formulations. To get the contact pair to work, the Details settings for Contact Shell Face and for Target Shell Face for the contact pair can either be left as “Program Controlled”, or set by the user to choices of Top and Bottom, so that the red Contact face and the blue Target face will look towards each other. Consequently, the Contact and Target surfaces do not face each other. The upper image in figure above shows a thickened view of the shell elements, so that closure of the gap is illustrated.Īs can be seen in the first figure above, the “Top” of each of these surface bodies happens to face in the –Y direction in the global coordinate system. These surface bodies are intended to lie on the midplanes of the shell elements, so in the example, both surface bodies have been set to a thickness of 4 mm, as illustrated in the figure below to the right. In this example, there is a 4 mm gap between the surface bodies. The shell thicknesses entered for the surface bodies in the model close the gap between the surface bodies so that they touch on a pair of faces. The figure above shows a pair of surface bodies, and the mesh that results when they have been meshed with shell elements.
Moi3d offset face of solid manual#
Either the tolerance employed in the creation of contact pairs will have to be modified, and the contact pairs regenerated, or manual contact pairs will need to be created between overlapping surface bodies. The gap size will often be greater than the tolerance used in the automatic creation of contact pairs when geometry is imported into Workbench Mechanical. If surface bodies are created on the midplane of the thin solids that they approximate, the surface bodies that lie on top of each other will have a gap between the midplanes.

This article examines a setup to employ with bonded contact across a gap between surface body midplanes in large deflection nonlinear analysis.Ĭreation of a Bonded Contact Pair Between Surface Body Faces Industrial Equipment and Rotating MachineryĪnsys Mechanical (Workbench) has many settings for contact between surface body (shell) faces.


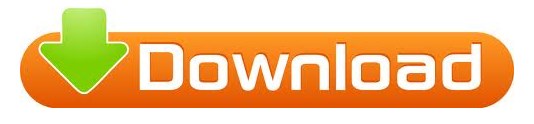